Can a single industrial accident, occurring on an ordinary day, forever alter the landscape of workplace safety? The Russian lathe accident of 1993, a catastrophic event at the Podolsk Machine Tool Plant in Moscow, Russia, stands as a stark testament to the potential dangers of industrial environments and the critical importance of preventative measures.
In the wake of incidents like the Russian lathe accident, industries worldwide have been compelled to reassess and elevate their safety standards. The implementation of comprehensive training programs is paramount, ensuring that workers possess a thorough understanding of the intricacies involved in operating machinery. This knowledge forms the bedrock upon which workplace safety is built.
Understanding the causes and the ripple effects of accidents like the one at Podolsk is not merely an academic exercise; it is an imperative for preventing future tragedies and guaranteeing the well-being of those who work in manufacturing, engineering, and similar fields. We must examine these events with meticulous detail, tracing the path from cause to consequence.
This article aims to dissect the Russian lathe accident, providing a comprehensive overview of its root causes, the devastating consequences that ensued, and the effective measures that can be deployed to prevent similar incidents. We will explore the specifics of the Podolsk disaster, examining the factors that contributed to the catastrophe and the immediate aftermath.
Implementing robust safety measures is of utmost importance in understanding the intricacies of the Russian lathe accident's causes, consequences, and recommended safety measures. These precautions involve a multifaceted approach, encompassing training, protective guards, routine maintenance, established protocols, and cultivating a strong safety culture, each component of which is vital in minimizing the risk of accidents and mitigating their impact. The absence of any one of these elements can create a vulnerability that puts workers at risk.
The Russian lathe accident, which occurred in 1993 at the Podolsk Machine Tool Plant in Moscow, Russia, was a devastating event. The machine failure resulted in the deaths of six workers and severe injuries to several others. This event underscores the need for strict adherence to safety protocols in manufacturing environments.
The tragic incident at the Podolsk Machine Tool Plant serves as a stark reminder of the potential hazards associated with machinery and the critical need for robust safety measures. It also highlights the necessity of continuous improvement in safety protocols and the importance of learning from past mistakes.
The accident took place during what seemed like a routine workday. A lathe operator was working on a piece when a critical element of the machine failed. The machine's rotating corridor faltered, causing severe injuries to the operator. This catastrophic failure underscores the critical importance of adhering to safety protocols in manufacturing environments.
The Russian lathe incident has become a pivotal case study in discussions about workplace safety and industrial accidents. It underscores the critical importance of adhering to safety protocols in manufacturing environments.
The Russian lathe accident is a tragic reminder of workplace dangers. The accident occurred due to inadequate safety measures and improper clothing. The Russian lathe accident serves as a stark reminder of the potential hazards associated with machinery and the need for stringent safety measures.
In 2023, a similar incident, although details may vary, underscored the enduring relevance of workplace safety and the crucial importance of adhering to proper operating procedures. The parallels to the 1993 incident serve as a critical reminder of the need for constant vigilance and a commitment to safety across all industrial settings.
This article aims to provide a thorough understanding of the Russian lathe accident, delving into its underlying causes, the immediate impact of the incident, and the valuable lessons we can derive to prevent future occurrences. As we analyze this tragic event, we will also examine the broader implications for safety standards in industrial environments.
By examining the specifics of the Russian lathe accident, we can gain insights into how to prevent such tragedies in the future. This involves a thorough examination of all contributing factors, from the initial machine malfunction to the overall safety culture within the plant.
The accident serves as a stark reminder of the importance of workplace safety and proper machinery handling. It also highlights the need for vigilance and the adoption of best practices to ensure the well-being of workers. Industrial accidents serve as stark reminders of the importance of workplace safety.
The Russian lathe accident highlights the importance of workplace safety and machinery handling. This incident serves as a crucial reminder of the potential dangers associated with industrial equipment, particularly lathes, which are commonly used in manufacturing and machining processes.
In this article, we will delve deep into the topic of Russian lathe accidents, exploring their causes, the consequences they bring, and the measures that can be taken to prevent them. These measures include comprehensive training, implementation of safety protocols, and the establishment of a culture that prioritizes safety above all else.
By understanding the causes of lathe accidents and implementing effective safety measures, we can prevent these incidents and ensure a safer working environment for everyone. We encourage you to share this article with your colleagues and peers to raise awareness about the risks of lathe operations and the importance of safety.
The Russian lathe incident has become a topic of significant discussion in recent years, especially in the context of workplace safety and industrial accidents. By adopting measures and guidelines implemented in other countries, Russia can enhance the safety and efficiency of lathe operations, thereby reducing the likelihood of accidents and improving the safety standards of the manufacturing sector.
The accident serves as a catalyst for change, driving improvements in safety protocols, worker training, and machine maintenance. It underscores the critical need for vigilance and the adoption of best practices to ensure the well-being of workers.
Essential safety measures to prevent lathe accidents; include implementing regular inspections, providing protective equipment such as safety glasses and gloves, and ensuring workers are adequately trained in machine operation.
Industrial accidents, such as the infamous Russian lathe accident, have long served as stark reminders of the importance of workplace safety. These incidents underscore the need for diligence, rigorous training, and a proactive approach to identifying and mitigating potential hazards. By understanding the causes of such accidents, we can work towards a safer working environment for all.
Understanding the Russian lathe accident is crucial for those in the manufacturing and engineering sectors. These accidents can have severe consequences, affecting not only the individuals directly involved but also the broader industrial environment. The ripple effects of such incidents can be far-reaching, impacting production schedules, employee morale, and the company's reputation.
This tragedy highlights the imperative to prioritize safety in all aspects of industrial operations. It reinforces the need for continuous improvement in safety protocols, thorough worker training, and a culture that places safety above all other considerations.
The Russian lathe accident demands a thorough investigation to understand the specific factors that contributed to the incident, enabling us to learn valuable lessons and prevent similar tragedies in the future. By examining the root causes and the resulting consequences, we can develop effective preventative measures and create a safer working environment.
By understanding the causes and effects of such accidents, we can prevent future occurrences and ensure workplace safety. Industrial accidents, such as the Russian lathe accident, have long served as stark reminders of the importance of workplace safety.
The tragic event at the Podolsk Machine Tool Plant serves as a stark reminder of the potential hazards associated with machinery and the need for stringent safety measures. This incident underscores the importance of continuous training, strict adherence to safety protocols, and a safety culture that prioritizes the well-being of all workers.
The Russian lathe accident occurred due to inadequate safety measures and improper clothing. The accident occurred in 1993 at the Podolsk Machine Tool Plant in Moscow, Russia. This event serves as a crucial reminder of the potential dangers associated with industrial equipment, particularly lathes.
This event highlights the importance of a strong safety culture within an organization. A culture that values safety will ensure that employees are properly trained, equipment is regularly maintained, and safety protocols are consistently followed. The tragedy serves as a powerful reminder of the human cost of industrial accidents.
The importance of worker training and certification in preventing lathe accidents cannot be overstated. Well-trained workers are better equipped to identify potential hazards, operate machinery safely, and respond effectively in emergency situations. Regular certification programs ensure that workers' knowledge and skills remain current.
Modern equipment and technology for safer lathe operations are playing an increasingly important role in preventing accidents. These advancements include features such as automated safety systems, enhanced guarding, and improved machine diagnostics. This technological progress is vital in creating safer and more efficient manufacturing environments.
Statistics and data on lathe accidents in Russia can provide valuable insights into the frequency, causes, and consequences of these incidents. Analyzing this information helps identify trends, pinpoint areas for improvement, and develop targeted safety interventions. Data-driven approaches are crucial for creating a safer working environment.
The legal framework for industrial safety in Russia establishes the rules and regulations that govern workplace safety. These laws and regulations define responsibilities, set standards, and provide a framework for inspections and enforcement. A robust legal framework is essential for ensuring that safety is a top priority in all industrial operations.
In response to incidents like the Russian lathe accident, industries have taken steps to enhance safety standards and prevent similar tragedies. Comprehensive training programs have been implemented to ensure workers understand the crucial aspects of operating machinery. This includes proper use of personal protective equipment (PPE), machine operation procedures, and emergency response protocols.
The Russian lathe accident stands as a critical example of how industrial accidents can impact not only the individuals directly involved but also the entire industrial sector. The need for stringent safety measures is of utmost importance in understanding the causes and consequences of the Russian lathe accident.
The accident highlights the need for a thorough investigation to identify the root causes of the incident. This includes examining factors such as machine maintenance, worker training, and the overall safety culture within the plant. The findings of such investigations are critical for developing preventative measures and preventing future tragedies.
The event highlights the importance of a strong safety culture within an organization. A culture that values safety will ensure that employees are properly trained, equipment is regularly maintained, and safety protocols are consistently followed. The tragedy serves as a powerful reminder of the human cost of industrial accidents.
Understanding the causes, consequences, and safety measures associated with the Russian lathe accident involves a multi-faceted approach. This includes a thorough investigation, the implementation of robust safety protocols, and a commitment to continuous improvement. By focusing on these key areas, we can reduce the risk of future incidents and ensure a safer working environment for all.
Comprehensive training programs have been implemented to ensure workers understand the crucial aspects of operating machinery. These training programs should cover a wide range of topics, including machine operation, hazard identification, and emergency procedures. Regular refresher courses and assessments are also essential to maintain competency and reinforce safe practices.
Modern equipment and technology for safer operations have become increasingly important in recent years. These technologies can include features such as automated safety systems, improved guarding, and advanced diagnostic tools. By embracing these advancements, industries can significantly reduce the risk of accidents and improve overall safety.
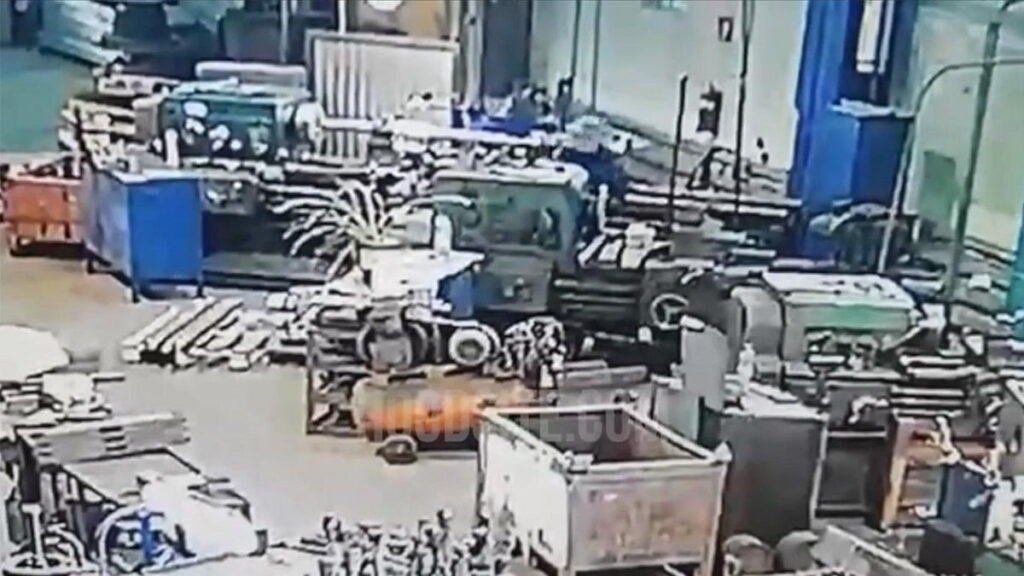

